Chemistry
Categories
Subscribe
About The Author
Nadim Maluf
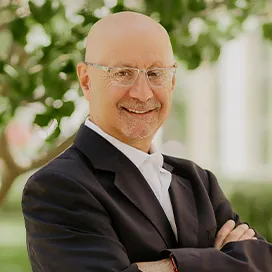
I am a consumer. I am an engineer. I innovate. I am inspired by others. I am a student. I am a teacher. I am a CEO. I admire great people who make great products. And I love it best when I make a difference in the lives of others.